ประการแรก วิธีการเป่าแก๊สป้องกัน
ปัจจุบันมีวิธีการเป่าแก๊สป้องกันหลักๆ อยู่ 2 วิธี วิธีหนึ่งคือเป่าแก๊สป้องกันแบบพาแกนิก ดังแสดงในรูปที่ 1 อีกวิธีหนึ่งคือเป่าแก๊สป้องกันแบบโคแอกเซียล การเลือกวิธีการเป่าทั้ง 2 วิธีโดยเฉพาะนั้นต้องพิจารณาในหลายๆ ด้าน โดยทั่วไปแล้วขอแนะนำให้ใช้การเป่าด้านข้างเพื่อป้องกันแก๊ส
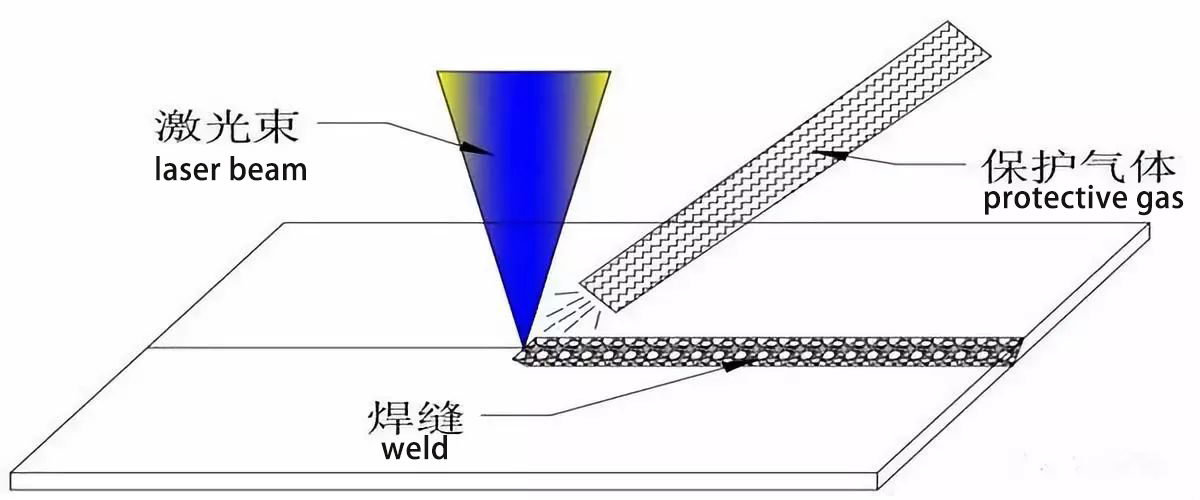
ก๊าซป้องกันแบบพาแกนเซียล
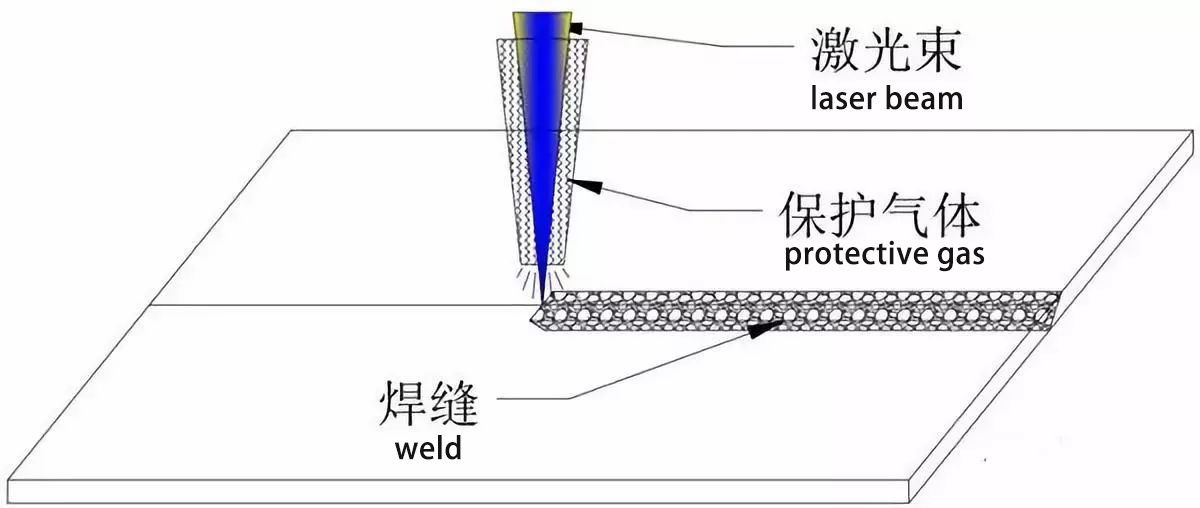
สอง หลักการเลือกโหมดการป้องกันการเป่าแก๊ส
ประการแรก ต้องชัดเจนว่ารอยเชื่อมที่เรียกว่า "ออกซิไดซ์" นั้นเป็นเพียงชื่อสามัญเท่านั้น ในทางทฤษฎีแล้ว หมายถึงปฏิกิริยาเคมีระหว่างรอยเชื่อมกับส่วนผสมที่เป็นอันตรายในอากาศ ซึ่งส่งผลให้คุณภาพของรอยเชื่อมลดลง เป็นเรื่องปกติที่โลหะเชื่อมจะทำปฏิกิริยากับออกซิเจน ไนโตรเจน และไฮโดรเจนในอากาศที่อุณหภูมิหนึ่งๆ
การป้องกันไม่ให้รอยเชื่อมเกิด “ออกซิเดชัน” คือการลดหรือหลีกเลี่ยงการสัมผัสของส่วนผสมที่เป็นอันตรายดังกล่าวกับโลหะเชื่อมในสถานะอุณหภูมิสูง สถานะอุณหภูมิสูงนี้ไม่เพียงแต่หมายถึงโลหะในสระหลอมเหลวเท่านั้น แต่ยังรวมถึงกระบวนการทั้งหมดตั้งแต่เวลาที่โลหะเชื่อมหลอมเหลวจนถึงการแข็งตัวของโลหะในสระและอุณหภูมิของโลหะจะลดลงจนถึงอุณหภูมิต่ำกว่าที่กำหนด
สาม ยกตัวอย่าง
ตัวอย่างเช่น การเชื่อมโลหะผสมไททาเนียม เมื่ออุณหภูมิสูงกว่า 300℃ จะสามารถดูดซับไฮโดรเจนได้อย่างรวดเร็ว มากกว่า 450℃ จะสามารถดูดซับออกซิเจนได้อย่างรวดเร็ว มากกว่า 600℃ จะสามารถดูดซับไนโตรเจนได้อย่างรวดเร็ว ดังนั้น รอยเชื่อมโลหะผสมไททาเนียมหลังจากการแข็งตัวและการลดอุณหภูมิลงเหลือ 300℃ ต่ำกว่าระยะนี้ จะต้องมีประสิทธิภาพในการปกป้อง มิฉะนั้น จะเกิดการ “ออกซิไดซ์”
จากคำอธิบายข้างต้นคงไม่ยากที่จะเข้าใจ การป้องกันแก๊สที่พ่นออกมาไม่เพียงแต่ต้องปกป้องแอ่งเชื่อมที่หลอมละลายในเวลาที่เหมาะสมเท่านั้น แต่ยังต้องปกป้องพื้นที่เชื่อมที่แข็งตัวด้วย ดังนั้น โดยทั่วไปแล้ว ให้ใช้แก๊สป้องกันแบบพาราเซียลตามที่แสดงในรูปที่ 1 เพราะวิธีนี้เมื่อเปรียบเทียบกับวิธีการป้องกันแบบโคแอกเซียลในรูปที่ 2 จะครอบคลุมมากกว่า โดยเฉพาะอย่างยิ่งสำหรับบริเวณเชื่อมที่แข็งตัวเท่านั้นจึงได้รับการป้องกันที่ดีกว่า
การเป่าด้านข้างแบบพาราแอกเซียลสำหรับการใช้งานทางวิศวกรรม ไม่ใช่ผลิตภัณฑ์ทั้งหมดจะสามารถใช้แก๊สป้องกันแบบเป่าด้านข้างของเพลาได้ สำหรับผลิตภัณฑ์เฉพาะบางอย่าง สามารถใช้แก๊สป้องกันแบบโคแอกเซียลได้เท่านั้น โดยมีความต้องการเฉพาะจากโครงสร้างผลิตภัณฑ์และรูปแบบข้อต่อที่เลือกเป้าหมาย
สี่ การเลือกโหมดเป่าแก๊สป้องกันเฉพาะ
1. การเชื่อมตรง
ตามที่แสดงในรูปที่ 3 รูปร่างของรอยเชื่อมของผลิตภัณฑ์เป็นเส้นตรง และรูปร่างของรอยเชื่อมอาจเป็นรอยต่อแบบชน รอยต่อแบบเหลื่อม รอยต่อมุมลบ หรือรอยเชื่อมแบบเหลื่อม สำหรับผลิตภัณฑ์ประเภทนี้ ควรใช้วิธีการเป่าแก๊สป้องกันด้านข้างเพลาข้างตามที่แสดงในรูปที่ 1
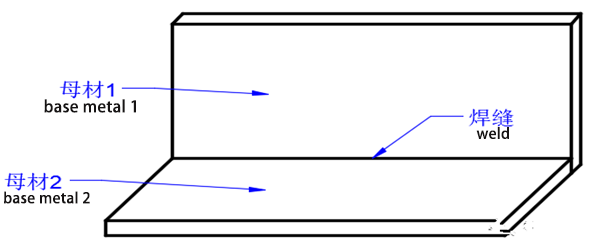
2. การเชื่อมกราฟิกแบบปิดแบน
ดังแสดงในรูปที่ 4 รูปร่างของรอยเชื่อมของผลิตภัณฑ์คือ รูปร่างเส้นรอบวงระนาบ รูปร่างหลายด้านระนาบ รูปร่างเส้นหลายส่วนระนาบ และรูปร่างปิดอื่นๆ รูปแบบรอยเชื่อมอาจเป็นรอยต่อชน รอยต่อซ้อน รอยเชื่อมซ้อนทับ เป็นต้น สำหรับผลิตภัณฑ์ประเภทนี้ ควรใช้โหมดก๊าซป้องกันแบบโคแอกเซียลดังแสดงในรูปที่ 2
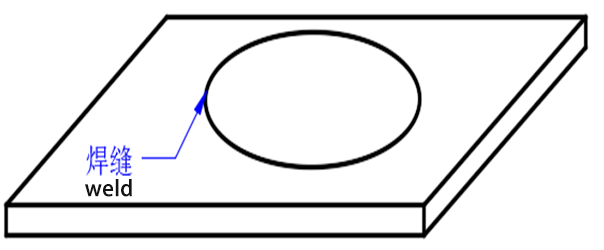
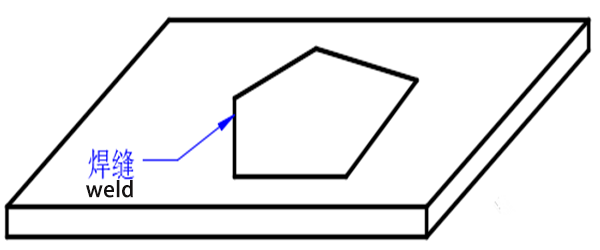
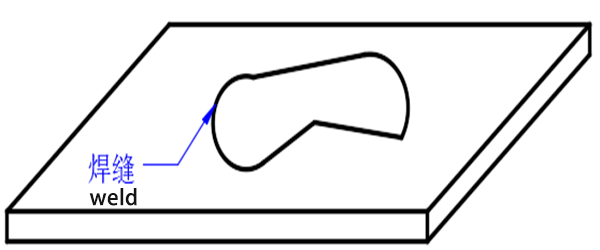
การเลือกใช้ก๊าซป้องกันส่งผลโดยตรงต่อคุณภาพการเชื่อม ประสิทธิภาพ และต้นทุนการผลิต แต่เนื่องจากความหลากหลายของวัสดุในการเชื่อม ทำให้ในกระบวนการเชื่อมจริง การเลือกใช้ก๊าซเชื่อมจึงมีความซับซ้อนมากขึ้น จึงต้องพิจารณาถึงวัสดุในการเชื่อม วิธีการเชื่อม ตำแหน่งในการเชื่อม รวมถึงข้อกำหนดของผลการเชื่อมอย่างครอบคลุม โดยผ่านการทดสอบการเชื่อม เพื่อเลือกก๊าซเชื่อมที่เหมาะสมยิ่งขึ้น เพื่อให้ได้ผลลัพธ์การเชื่อมที่ดีขึ้น
ที่มา: เทคโนโลยีการเชื่อม
เวลาโพสต์: 02-09-2021